Laser Assisted Tape Winding (LATW)
The laser assisted tape winding technology is enabling the manufacturing of composite products with a high level of automation. The combination of a standardUD-Tape, with fibers embedded in a thermoplastic matrix, and a high power laser beam to heat the material, allows manufacturers to process multiple materials and achieve high productivity rates..
The laser assisted tape winding is part of the Automated Fiber Placement (AFP) technology (more specific called ATP: Automated Tape Placement) together with the laser assisted tape laying for sheet and 3D-curved shapes. Laser Assisted Tape Placement and Laser Assisted Tape Winding are grouped under the term Laser Assisted Tape Deposition (LATD).
The laser assisted tape winding technology is commonly seen as a breakthrough for the application of thermoplastic composite products for mass production and large series due to the high automation capability combined with the laser capacity for high productivity.
How does the technology work?
This technology is using the capability of thermoplastics to become soft at a certain temperature, by heating the material with a laser beam. In the figure to the right, the laser assisted tape winding process is depicted in detail. Around the mandrel, which determines the inner shape of the tube, the UD-tape is wound by rotating the mandrel while the laser heats directly the tape and a part of the substrate. The substrate is in general the already produced layer(s) on the mandrel. By using the laser power to accurately heating the mixed zone of UD-tape and substrate, the material can be weld together at a high speed. The compaction roller will immediately put pressure on the welding zone and cool the area to result in a perfect weld between tape and substrate..
The angle between the mandrel and the UD-tape, is determining the reinforcement direction of the tube. Mixing several angles/layers will result in a more or less isotropic behaviour of the material. Focussing on for instance 45 degrees angles will improve the torsion stifffness of the tube. This way the tube can be optimized for the specific function in a product or machine while minimizing material consumption.
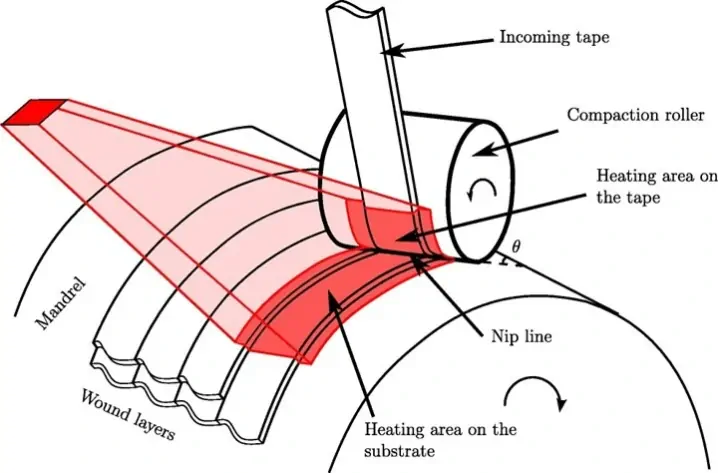
What are the possibilities of the LATW technology?
As I have already indicated, this technology is applied to manufacture thermoplastic composite products. This type of composite material is 100% recyclable and fits perfectly in the 3R model: Reduce, Reuse and Recycle.
The technology can be applied for a large group of thermoplastics that are available as UD-tape. Most of the UD-tape suppliers deliver these tapes with carbon fiber and/or glass fiber. Also other fibers like aramid or biobased fibers are in some cases available. Interesting development from the sustainability point is the application of biopolymers as thermoplastic matrix in UD-tapes although this is still in an early development stage.
Written by Theo Mimpen, September 2021
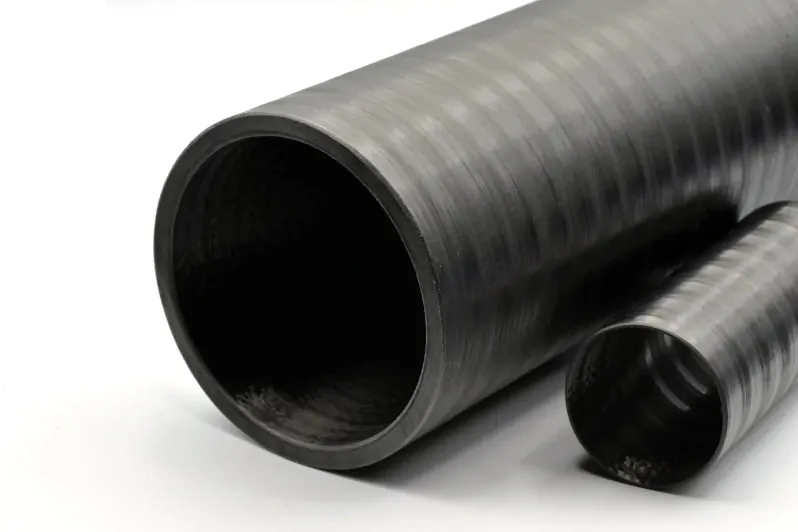
Frequently asked questions
Laser Assisted Tape Winding (LATW), an Automated Fiber Placement (AFP) technology
> What makes laser assisted tape winding (LATW) interesting compared to other processes to produce FRP products?
The most common processes to make FRP products are most of the time very labour intensive and therefore not suitable for mass production. These processes are often difficult to automate and require multiple steps. Laser assisted tape winding is a so called AFP (automated fiber placement) technology and like laser assisted tape laying, it has the advantage that the technology can be automated. In robotised or CNC-automated cells, the process takes care of the manufacturing of products and allows the flexibility to produce many different type of products in one cell. The laser power enables high productivity of the manufacturing process. A major advantage is, compared to the technologies to process fibre reinforced thermoset material, that there is no need for an additional curing step. This simplifies the manufacturing process and prevents high investment in specialised autoclave equipment.
> For which markets and applications is laser assisted tape winding developed?
The laser assisted tape winding technology is originally developed by Boeing. After that AFPT GmbH took the challenge to bring the technology to industrial level. The technology enables the automated production of fiber reinforced thermoplastic products like tubes and rings, mainly for high demanding applications.
Examples are:
- drive shafts (power transmission)
- frames for solar panels on sea (structural elements)
- hydraulic cilinders (pressure containment)