Connections with CFR Thermoplastics
Our CFR Thermoplastic tubes are always part of a product and must be connected to other elements or parts. And like with metal there are many and remarkably similar options to make that connection depending on the required function and load conditions. For example, when a tube is part of the pressurized system, the connection must prevent leakage and resist the pressure of the liquid that is contained.
Like you can read in my blog about Additive Manufacturing with Laser Windingworking with CFR thermoplastics invites you to optimize your design by understanding the requirements of the function and load conditions.
For the connections to other parts or elements of your product, the same approach is preferred: add material where required to create a connection or bond instead of removing material. Or at least be aware when removing material that the optimized design is to be compensated locally to maintain the function and load as designed for. I will present some of the available technologies in two categories: Connections (or joins) without and with removal of material.
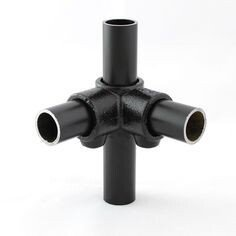
Connection/join without removal of tube material
The possibilities to make connection to other parts, depend first on all to the type of material you are connecting with. Secondly the strength of the connection is determined by the function and load condition. The designer is challenged to simplify the overall design and balance the costs of production, assembly, and maintenance of the product.
You can split this group into bonding and clamping, which is based on friction/force. As CFR Thermoplastic tubes are specifically interesting for high load situation, I will give here some examples of the technologies to make a strong connection:
BONDING WITH ADHESIVES
Adhesives are available for many types of materials and material combinations (like metal to CFR composite material). The adhesives are offered by several (global operating) manufacturers and they offer guidance for the specific requirements. Adhesives have replaced many fasteners in the automotive manufacturing industry, which shows the potential of this type of connection in relation to the strength and safety requirements.
WELDING
Thermoplastic material is perfectly suited for welding. The general rule is to weld the same thermoplastic material to one another but the are some combinations of different thermoplastics possible. A whole range of welding technologies like:
- laser welding (also used in our tube manufacturing process);
- friction (stir) welding;
- ultrasonic welding;
- resistance welding (not applicable on carbon fibers)
- induction welding (only applicable on carbon fibers; see also video of TPRC)
are available in the market and are based on heating the welding zone using an external heating device. Another option is solvent welding, where the contact area is temporarily dissolved to be able to create a mixed zone of the two attached surfaces.
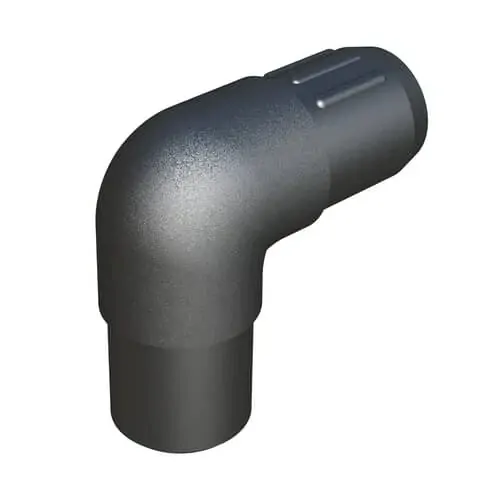
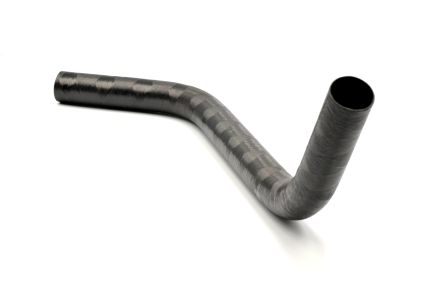
RESHAPING THROUGH THERMOFORMING
Another interesting thought is to reduce or simplify connections with other material by reshaping the CFR thermoplastic tube. One of the advantages of thermoplastics over thermosets is that it can be reshaped when is heated to a specific temperature. That temperature depends on the type of thermoplastic material applied. It offers the possibility to reshape the tube and add a flange at the end of a tube to make a closure. Or to reshape the round end of a tube to a square end, fitting to a similar shaped part and able to transfer the static or kinetic energy. Another option is to bend the tube to eliminate the need for another part, saving costs and simplifying the whole design of your product.
OVERMOLDING
This technology is a perfect example where the same base material is used to create a connection. Overmolding allows to bond the thermoplastic material of two parts through the application of injection molding. You can read more about overmolding in my blog called Inserts and Overmolding.
Connection/join with removal of tube material
FASTENERS
The most common way to connect two parts is to use ‘bolts and nuts’. It means that you need to remove material and make a hole or slot in the CFR thermoplastic tube. There are two main categories of fasteners:
- threaded: bolts and nuts
- unthreaded: (split or tapered) pin.
The big advantage of fasteners is that they can be removed or dismantled to take the parts apart from each other.
Other connections
There are obviously many more options to create a permanent or dismountable connection, with and withour removal of tube material. Also combinations of the mentioned connections can be applied to create the desired strength and cost effective solution.
All the mentioned options are just examples of many more available technologies but are believed to be the most relevant for the CFR Thermoplastic tubes that are produced by Alformet.
Written by Theo Mimpen (April 2021)